When selecting the best cutting application for your needs, it is important to have a thorough understanding of the different methods available to you. Some cutting methods are better for extremely detailed and fine work, while others may be more equipped for thick materials. The most common cutting methods available on the market today are waterjet cutting, wire EDM cutting, laser cutting, and plasma cutting.
Waterjet cutting uses a high pressure stream of water mixed with an abrasive to cut materials into the desired shape. It is particularly valuable for its ability to provide accurate cuts without applying heat to the material as well as its ability to cut nearly any material. Wire electrical discharge machining (EDM) is a very specialized process in which an electrically charged strand of wire passes through the workpiece, causing an electrical discharge from the wire that erodes the metal in a very controlled and accurate process. Laser cutting is done by focusing a high-power laser beam at the workpiece to remove material by melting and vaporizing it, creating a smooth precise cut. Plasma cutting, which can only be performed on conductive metals, uses an extremely hot, high-speed jet of plasma to cut through the material.
Each of these cutting processes offers a different set of benefits and uses. While waterjet cutting is by far the most versatile cutting method, the EDM, laser, and plasma cutting methods provide their own benefits for particular products and applications. In this blog, we compare the different cutting methods and their benefits to help you determine which process works best for you.
Waterjet vs. Laser Cutting
Laser cutting is faster and cheaper when cutting thinner materials, but it has more material restrictions than waterjet cutting. Waterjet cutting can be used to shape nearly any material, including metal, plastic, glass, rubber, and stone. Since laser cutting uses heat to cut, it is mostly limited to cutting metals. However, some plastics, composites and other materials like wood and foam can be cut with a laser but with reduced thicknesses. Lasers vaporize the material, which in some non-metal materials causes fumes that can be quite toxic. Some metals are also challenging to cut with a laser, including copper, brass, manganese, nickel, and lead.
While laser cutting is more precise when cutting detailed or intricate patterns, it cannot cut through very thick materials the way waterjets can. Waterjets have no difficulty cutting materials that are too thick to cut in almost any other way. Lasers can cut fast in thinner metals and have a narrow kerf, making them suitable for cutting parts with fine detail. However, it is important to note that since laser cutting produces heat, detailed parts can overheat and warp, whereas waterjets produce almost no heat at all.
Waterjet vs. Plasma Cutting
Plasma cutting uses a high velocity jet of plasma to cut conductive metals. It is an extremely quick method and has a lower operating cost than the other cutting methods. It is also far less precise than laser and waterjet cutting. The heat from plasma cutting can also warp or distort the edges of the cut material, which makes it unsuitable for fine or detailed work. Overall, plasma cutting works as an option for quick, inexpensive cuts that do not require a great deal of precision. If you require more precise and detailed cuts without the risk of edge deformation, waterjet cutting is the better choice.
Waterjet vs. Wire EDM Cutting
Wire EDM machines can cut thin as well as thick metals with precision far surpassing anything achievable by any other cutting process. Parts can be produced that are accurate within tenths of a thousandth, removing the need for secondary machining processes. The downside is that wire EDM is a very slow process and is more expensive than waterjet cutting in cases were waterjet tolerances and surface finish are acceptable. Wire EDM is also limited to only metals, whereas waterjets can cut nearly any material. Ultimately, choosing between EDM and waterjet cutting is a question of what tolerances and surface finish are required. For products that need to be completed quickly and do not require machined-quality precision, waterjet cutting is ideal. Even when the part needs to be machined, in many cases waterjet cutting a near net shape to remove the bulk of the material and then machining to size is still cheaper than wire EDM.
Contact the AquaJet Team to Learn More
When compared with other cutting methods, waterjet cutting offers superior cutting accuracy for the widest range of materials and thicknesses. It is relatively inexpensive and produces very little waste. The process can be used to cut materials that would warp or deform with other methods. It is certainly not the best tool for every job, but it is a very versatile option that cannot be beat in many applications. AquaJet specializes in quality waterjet solutions for a broad range of industries and applications. To learn how you can use waterjet cutting for your next project, contact us today!
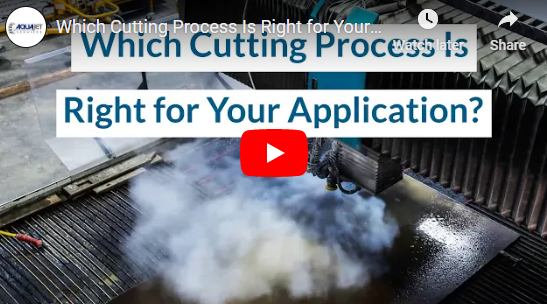