Waterjet cutting is an incredibly versatile method used to shape components from a variety of materials. One of its primary benefits is the ability to cut particularly thick materials. With waterjet cutting, thick steel and other materials can be cut accurately and efficiently. Here, we will discuss the potential limitations of waterjet cutting for thick materials, its benefits over other methods, and some tips to ensure quality cuts.
Potential Limitations
Although waterjets are in many ways ideal for cutting thick materials, the process presents some limitations. Material thickness affects the accuracy of the cut in ways that can compromise the final product, so it is important to use a waterjet service provider who understands these limitations and ways to mitigate them. The most common limitations when cutting thick materials include:
Reduced Accuracy: Greater thickness can result in lower accuracy. In the same way that the accuracy of a gun is decreased the further the bullet gets from the barrel, the cutting accuracy of a waterjet is also decreased as the water and abrasive particles get further from the cutting head. As the thickness of the material increases, tolerances must be expanded to account for reduced accuracy.
- Near Net Shapes: Due to reduced accuracy at greater thicknesses, it is sometimes necessary to cut to a near net size, allowing for some additional processing in order to meet the required tolerance and surface finish.
- Deeper Striations: A waterjet cut surface consists of an upper smooth zone and a lower rough zone, with the rough zone characterized by a distinctive pattern of wavy striations. In any thickness, the striations become more pronounced as the cut speed is increased and can be lessened, or completely eliminated, by cutting more slowly. However, in thicker materials, the striations become deeper and more noticeable and it becomes increasingly cost prohibitive to eliminate the striations by slowing down.
- Longer Production Time: The thicker the material, the slower the cut speed, with cut speeds decreasing exponentially as the thickness is increased. For example, 18” thick steel cuts at almost half the speed of 14” thick steel, even though there is only a 28% increase in thickness. This is the greatest limitation when using waterjet cutting for thick materials.
Advantages
Despite its limitations, waterjet cutting remains one of the most useful methods for cutting thick materials. In fact, it offers numerous advantages over other cutting methods, including:
- High Quality Cuts: Waterjet cutting can produce high quality parts from thick materials to a high degree of accuracy, without exposing the material to heat.
- Raw Material Savings: Raw materials can be used very efficiently by nesting parts closely together and in some cases even sharing the same cut between two different parts.
- No Thermal Damage: Since the waterjet cutting process does not generate heat, there is no risk of modifying the properties of the material or warping of the part due to heat.
- Speed: Although waterjet cutting of thick materials can take more time, all cutting methods require extensive time to cut through thick materials. Actually, waterjet cutting is significantly faster and cheaper than wire EDM, which is its main competitor in thick metal cutting. When compared with other conventional cutting methods, waterjet cutting often offers superior results for overall production in spite of being a slow process.
- Material Thickness: Waterjet cutting can be used to cut extremely thick materials that would be extremely difficult or impossible to cut using other methods.
Here are some things to consider when choosing a cutting process:
- Material Composition: Consider the properties of the material and the risk of cracking, warping, and breakage. Waterjet operators calibrate the pressure and speed according to the specific material makeup to ensure ideal cutting accuracy without the risk of damage to the material.
- Product Design: Determine the design size, complexity, and level of detail necessary for the product. Waterjet cutting can be used to cut thick materials to net or near net shapes without introducing stress to the part.
- Cost Savings: When budgeting for your project, consider the amount of raw material, expected waste, and consumable materials that will be used in the process. Waterjet cutting produces less scrap and requires very little consumable material.
- Programming, Setup, and Maintenance: In addition to cutting time, consider the amount of time it will take to set up, program, and maintain the cutting apparatus. You will find that waterjet cutting requires very little setup time and can easily be programmed for multiple jobs without significant downtime.
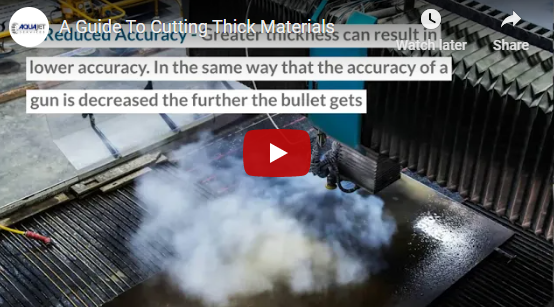
Contact the AquaJet Team to Learn More
AquaJet is pleased to offer custom waterjet cutting and fabrication services for a wide range of materials and thicknesses. To learn more about our quality waterjet cutting services, contact us today!